Med 3D-printning öppnas nya dörrar
Man måste våga. Det är inte alltid det fungerar, men har man inte provat så vet man inte.
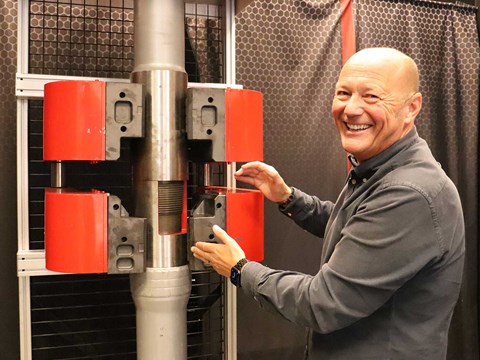
Printade i rostfritt stål
Totech Industriutveckling AB i Billingsfors, Bengtsfors kommun, levererar tekniska lösningar inom produktionsteknik, produktion och automation. Den största delen av deras verksamhet ligger sedan många år tillbaka inom offshore-branschen.
En av deras produkter är ett 6,8 kilo tungt ventilblock i aluminium och företaget tog i år steget att printa just det i rostfritt stål.
Intresse av att testa 3D-tekniken
Vi träffar två av Totechs frontfigurer Tommy Tveter, vd, och Robert Aronsson, konstruktionsansvarig, som varit med sedan företaget grundades på 90-talet. Båda är nyfikna och har stort teknikintresse och blev, så snart tekniken med 3D-printning fått fäste, intresserade av den. Detta kom fram när vi från IUC Väst besökte företaget och tipsade om att det fanns möjligheter att testa på tekniken.
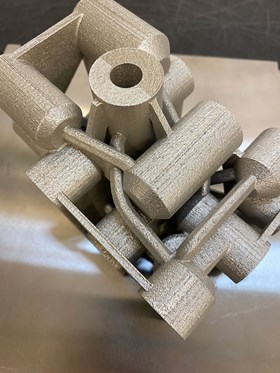
3D-printa istället för att borra
Efter samtal med Håkan Hellström på IUC Väst och experter på RISE, samt ett studiebesök på Applikationscenter för additiv tillverkning (AM-center), stod två saker klara för Tommy och Robert – de ville medverka i 3D-Action och ville testa att printa ett ventilblock.
– Det finns ju bara raka borr – de är åtminstone raka när man börjar borra, säger Tommy med ett leende. I ett vanligt hydraulikblock måste man borra, och en del av kanalerna är väldigt svåra att borra.
Detta var en av anledningarna till att just ventilblocket var en god kandidat för 3D-printning och det fanns fler.
Svår miljö
Miljön där ventilblocket används är svår med saltvatten och frätande borrvätska. Det är ett plus med en ökad korrosionsbeständighet på materialet men det blir både för tungt och för dyrt att tillverka blocket i något annat än ytbehandlad aluminium.
Dessutom var en annan faktor som talade för en ny tillverkningsmetod att Totech kämpade med mycket långa leveranstider på delkomponenter, ibland nästan 400 arbetsdagar.
– Nu har vi kunnat tänka till och plocka bort en hel del komponenter, så att blocket blir bättre, mindre och smidigare. Vi printar det i rostfritt stål, vilket är en stor fördel eftersom det får högre resistens. Hade vi tillverkat det gamla blocket i rostfritt hade det nog vägt runt 15 kilo, men det nya printade blocket väger bara 2,4 kilo, en tredjedel av det gamla blockets vikt, säger Tommy.
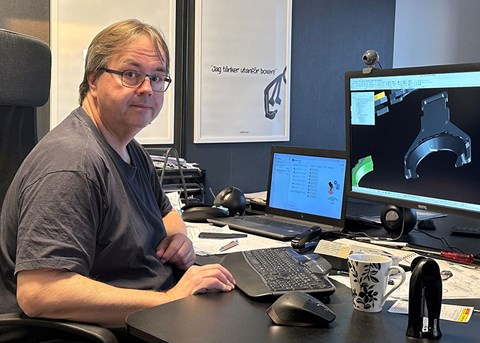
Framgångsrik printning
Ventilblocket printades framgångsrikt på Chalmers Tekniska Högskola under 3D-Actions slutfas.
Film och foto: Rasmus Gunnerek, Chalmers
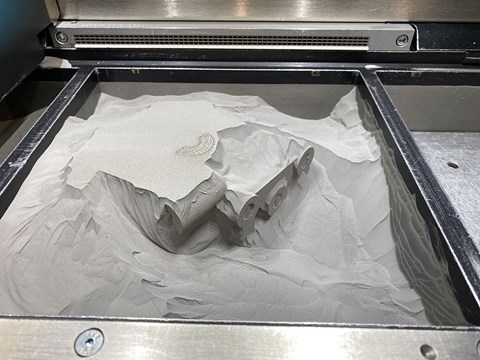
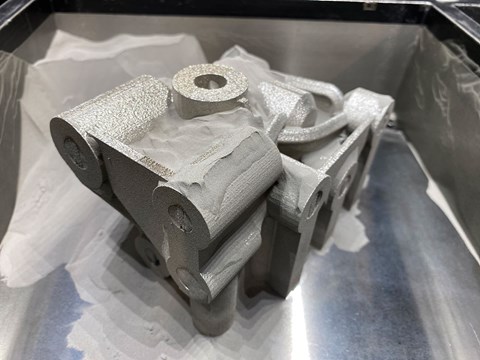
Nästa steg för Totech
Totech har beviljats ett FoU-kort från Västra Götalandsregionen för att fortsätta sin resa inom additiv tillverkning, ett direkt resultat av att ha varit med i 3D-Action. Både Tommy och Robert tror och hoppas på att kunna 3D-printa fler komponenter med bättre egenskaper än sina traditionellt tillverkade motsvarigheter i framtiden.
– Ventilblocket hör ju till hydraulik, men vi gör även pneumatik. Pneumatiken har inte lika hög leveranstid, men det krävs väldigt mycket monteringstid. I dag måste vi fräsa ut en aluminiumlåda som vi sätter allt i, för pneumatikkomponenterna är inte gjorda för den korrosiva miljön. Lådan är inte gratis att göra, med slangar och allt. Mycket av detta tror jag att vi skulle kunna printa i stället, säger Robert Aronsson.
Deltagandet i 3D-Action har enligt Tommy och Robert varit avgörande för de framsteg de kunnat göra inom 3D-printning.
– Hade det inte varit för projektet hade vi inte gjort det här. Möjligheten att spåna idéer med IUC Väst och RISE, samt att besöka AM-verksamheten i Mölndal har varit helt avgörande. Genom att gå runt och titta på alla printmetoder som finns och de delar som gjorts förstod vi vad som var möjligt, säger Tommy.
Uppmaning till andra företag
Tommy och Robert säger så här till andra företag med produkter som potentiellt skulle kunna 3D-printas:
– Man måste våga. Det är inte alltid det fungerar, men har man inte provat så vet man inte. Det är superbra att göra ett studiebesök, så att man får en inblick i vilka tekniker, möjligheter och resurser som finns. Man kan relatera till den egna verksamhet när man går runt och tittar, det är då idéerna kommer.
Många förknippar nog 3D-printning med något man har för hobbybruk, men det går att göra så mycket mer.
Totech Industriutveckling AB är ett av IUC Västs medlemsföretag och har i sitt 3D-printningsprojekt fått stöd genom Industriell Dynamik och 3D-Action.
Här läser du mer om:
Mer information
Är du också intresserad av 3D-printning? Kontakta då Håkan - hans kontaktuppgifter ser du här bredvid!